Are you thinking about putting a beer separation in your brewery?
We give you 5 reasons why this is the right investment.
1 – Go faster to the market
Separators or centrifuges allow you to get to market faster by cutting storage time and without the need to invest in new tanks. The brewing production is faster with less intermediate stops for cleaning, that means you will save labor and therefore money.
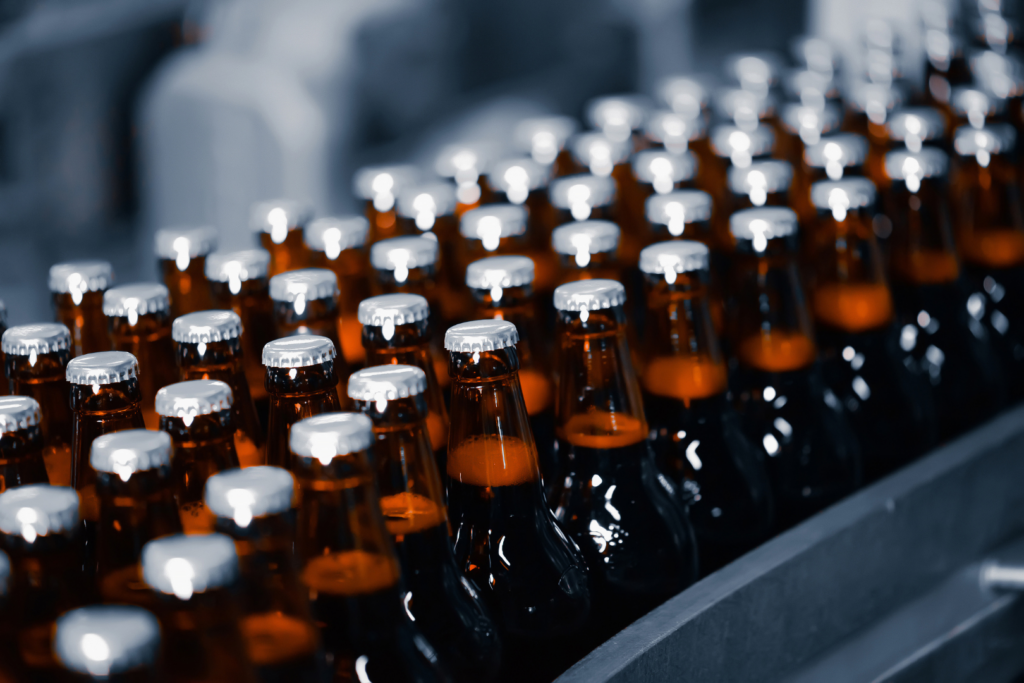
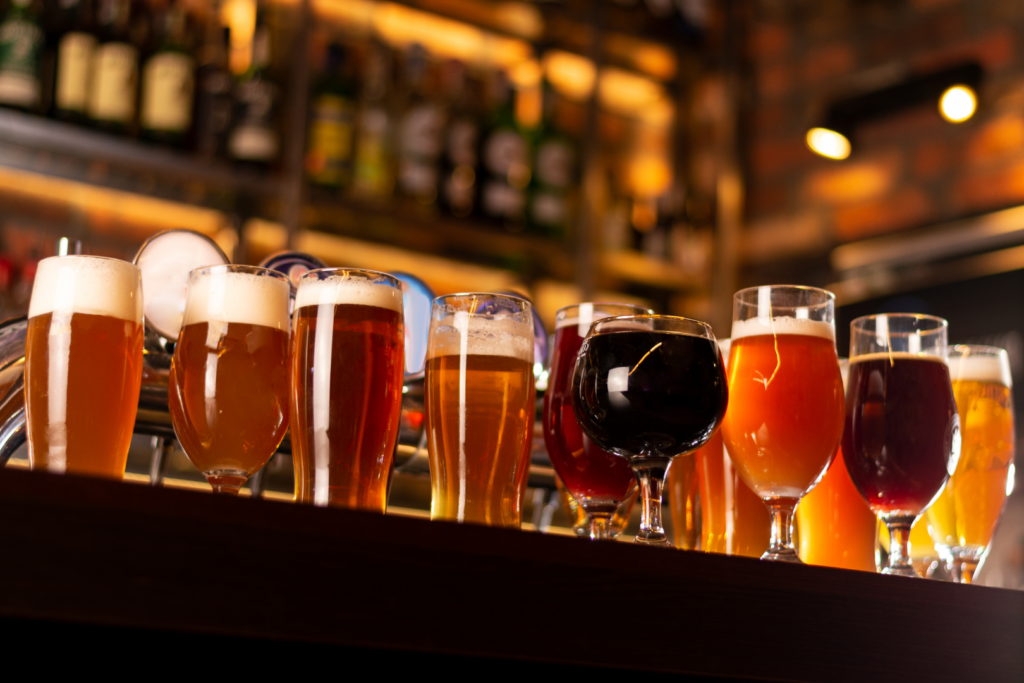
2 – Diversify your beer offering
With a separator you can obtain both some haze or a brilliantly clear beer. Multi-purpose applications in the brewing process to take your business to the next level:
– Non-filtered beer with the possibility to adjust the desired level of turbidity
– Filtered beer even without passing through a filter.
– Filtered beer as with a crossflow filter only by adding cartridge or disc filtration.
3 – More brewed beer with less effort
In the cleaning process of unfiltered beer, compared to traditional filtration, you can produce up to 10% more beer from the same amount of raw ingredients. No product will be loss in filter cartrdige clodging. With classic disc filters you cannot process beer because they would get clogged immediately; on the other side the alternative would be a tangential filter, but filtration level cannot be adjusted, and only filtered beer can be produced.
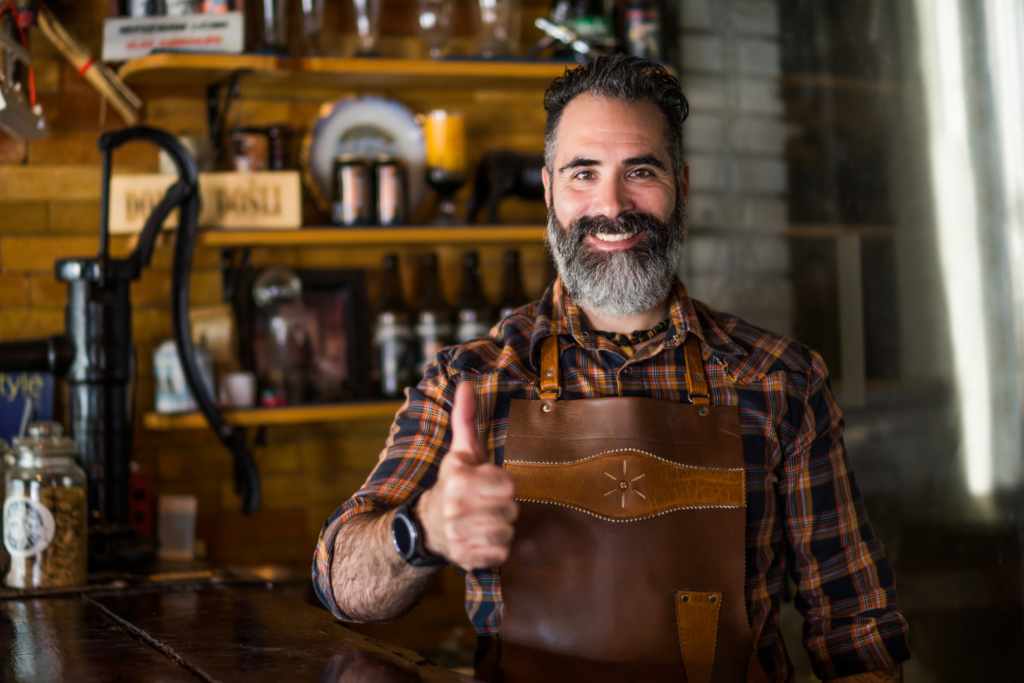
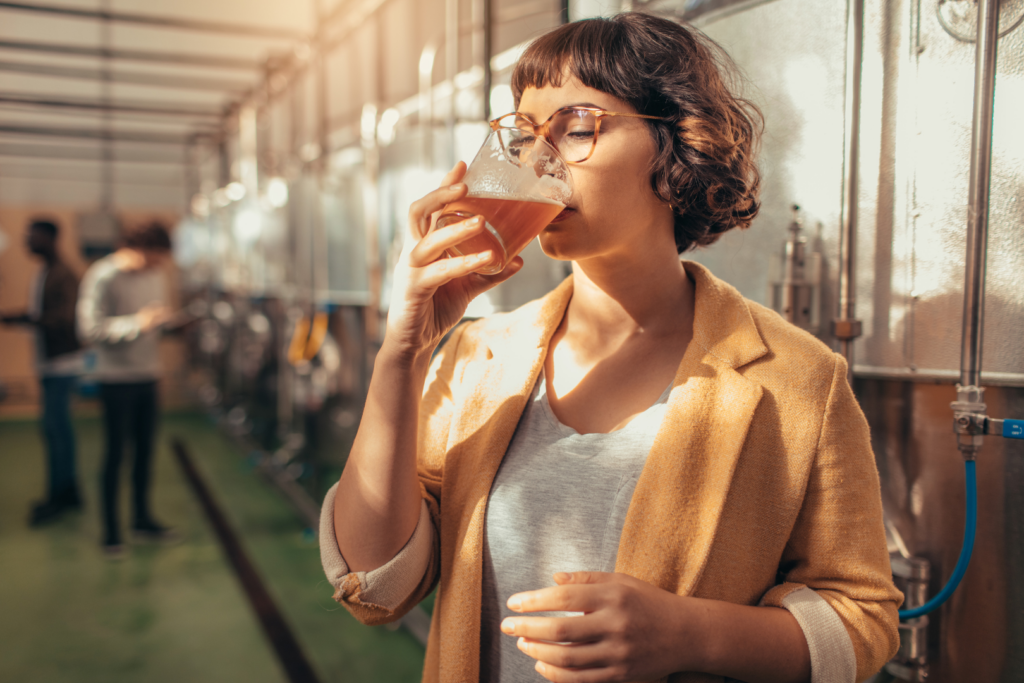
4 – Improve organoleptic characteristics and shelf-life
Filtration by means of centrifugal separation enhances beer quality and achieves the same consistency in each beer type. You will not have hops or yeast residues in your beer, while the aromas and flavour will be improved in each batch.
Shelf-life is easily extended.
We know needs and challenges of craft brewers, that is why our RE-BR serie guarantees zero oxygen absorption and gentle treatment ot the product.
5 – No oxygen absorption for a perfect beer foam: With the innovative ZeroOxTM system, no oxygen pick up will occur; it makes the centrifuge as hermetic as if it were made with mechanical seals but has no wear or need for maintenance. The system is so high performing that, in many cases it even lowers the level of oxygen present in the incoming beer.
At the same time, the “Soft” feeding and separation system does not break the protein chains, which are important for foam and its maintenance over time.
Every beer is different and therefore the brewing industry has specific requirements. The use of centrifugal separation technology makes it possible to optimise and standardise brewing processes and can lead to further potential savings.
Watch the video to discover more